OPTIMISATION AND PROPOSALS
AUTOMATION OF A SELECTED ASSEMBLY PROCESS
“Cooperating with Asseco CEIT, together with our joint work on the manual assembly project, was of great benefit to our team. I appreciate the fact that we were able to involve the assembly line staff in the project, and their suggestions were incorporated into the suggested solutions”
Peter Lacko
IMS & CIS Leader, ZF Active Safety Slovakia
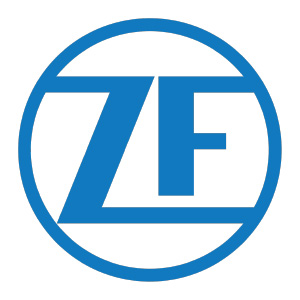
Customer: ZF ACTIVE SAFETY SLOVAKIA S.R.O.
Industry: Automotive
Focus: Assembly of control systems and electric motors for power steering
Location: Production plant Nové Mesto nad Váhom, Slovakia
Asseco CEIT solution: Avix, dynamic simulation, industrial ergonomics
ZF is a technological corporation active worldwide which supplies mobility for cars, utility vehicles and industrial technology.
Project background
The objectives of the project were to suggest measures to eliminate losses and waste on the electric motor winding workplace, to identify the potential for increasing productivity and to work on proposals to reduce the ergonomic burden on staff. This was followed by the development of three levels of optimisation for different levels of automation and financial costs.
Solution
The solution was divided into four phases: from a rough analysis of losses to the preparation of proposals for automating the workplace.
1st phase: Collecting all the necessary data, which was then processed using the AviX software. The rough analysis of losses, based on video sequences of individual work processes, helped define potentials for increasing work productivity by up to 49%.
2nd phase: Processing MTM analyses using the MTM-1 method, which is particularly suitable for optimising short work cycles. Based on this analysis, the process losses resulting from a non-uniform execution of operations were defined in cooperation with the training centre, followed by objective work and time standards.
3rd phase: Information obtained from the MTM analysis was used in a workshop, where a joint Asseco CEIT and ZF work time generated over 40 measures to increase work productivity and to partially
reduce the ergonomic burden.
4th phase: Asseco CEIT prepared a rough concept of the possibilities of automating selected processes, including a visualisation. Potential solutions were presented at three levels, from a low-cost solution using slanted shelving and roller conveyors, to a design using collaborative robots and automated conveyor belt systems.
Project output
One of the many project outputs was the specified need for an in-depth ergonomic analysis of selected processes, since this is a physically specific process which replaces full automation using current technologies.
Project benefits:
setting out
optimal
work methods and conditions
creating objective time standards
using the
MTM-1
method
defining an action plan for a realistic
increased work productivity of up to
40%
creating concepts for the
low-cost
mechanisation and automation of
selected processes with a calculated
payback ranging from 2 to 27 months
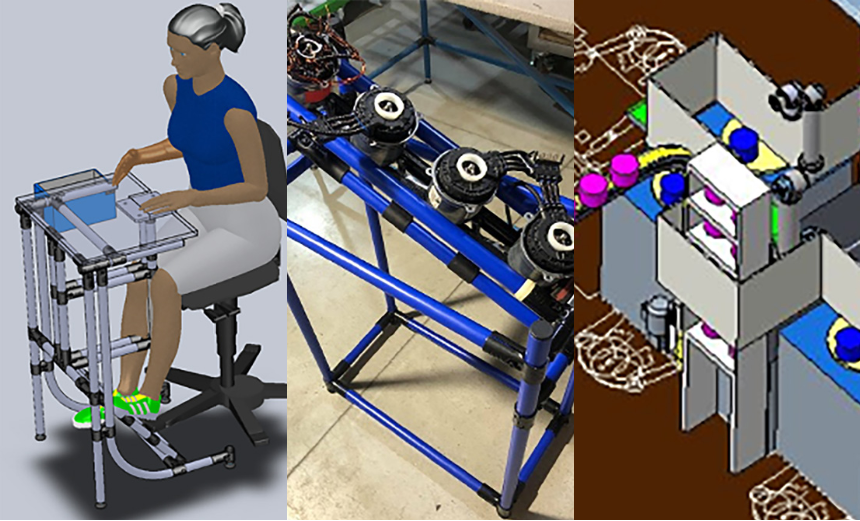
Potential
For increasing work productivity up to 49%