Digitalization in the automotive industry
using state-of-the-art technologies
“Thanks to the deployed superstructure control system from the workshop of the technology company Asseco CEIT, we achieved a 20% difference in the OEE fleet of forklift trucks in the warehouse premises of the press shop, as well as a high increase in the utilization of the mentioned warehouses. We also appreciate the reliability of the supplier and its solutions because the visualization of the fleet in real time has brought us increased safety in the workplace.”
Martin Adamička
Plant Logistics Manager, Volkswagen Slovakia
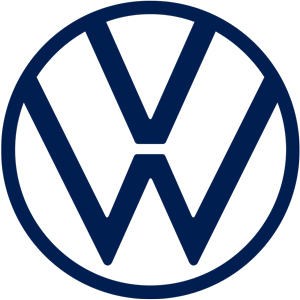
Industry: Automotive industry
Focus: Production of cars of 5 brands of the Volkswagen concern
Location: Volkswagen Slovakia production plant in Bratislava, Slovakia
Asseco CEIT solution: Twiserion Design Manager, Twiserion Digital Manager
Volkswagen Slovakia is the only car plant in the world to produce 9 models of vehicles of five brands under one roof: Volkswagen, Audi, Porsche, SEAT and ŠKODA. More than 99% of production is exported to more than 150 countries around the world.
The production plant of the German carmaker Volkswagen in Slovakia produces more than 300,000 cars every year. With such a volume of production, the group needs to focus its activities on increasing the efficiency of processes. One of the answers is digitization in the form of a modern location system and a digital twin, i.e. an identical twin of a real company in digital form. The aim of the digitization project was clear in this case: to increase efficiency and save operating costs through innovation.
Future = Innovation + Digitalization
Asseco CEIT has created an intelligent location system for the future in Volkswagen Slovakia, where data on the movement of means of internal logistics is automatically collected. The collected data is used by the company to continuously optimize the movement, display of position in real time, forklift occupancy, traffic density and the emergence of bottlenecks, accident and injury prevention, simulation of various crisis situations and more.
When difficult conditions lead to sophisticated solutions
Although the environment of the production hall may appear to be clean and organized, the complexity of the development presents several obstacles for the localization system. The presence of metal structures (racks, machines, etc.) can confuse a system built on common technologies (WiFi, Bluetooth). Therefore, Asseco CEIT deployed an industrial solution for transmitters and receivers based on UWB technology at the Volkswagen Slovakia plant in Bratislava, which ensured stable data collection on the movement of internal logistics even in such a “complex” environment.
The variability of storage space utilization was also a challenge that Asseco CEIT had to deal with. Where there is a pallet of material one day, there may be an empty area the next. This was also one of the reasons why UWB technology was ideal both in terms of coverage and because it offers high localization accuracy, so there is no overlapping of positions.
Navigation in the production shop?
In order to optimize the processes in the production shop, it is possible to use the smart sensor network for another sophisticated solution, the purpose of which is to optimize the routes of forklift technology and reorganize warehousing. Thanks to this solution, optimal delivery of material is ensured with regard to the current “traffi c“, whether at intersections or within the utilization of the logistics route.
Part of the solution for Volkswagen Slovakia was the deployment of the ELLA platform for displaying the collected data. This platform enables clear display of the positions of internal logistics resources both in real time and in the past. Thanks to ELLA platform, managers at Volkswagen Slovakia can make the right decisions based on always relevant data.
Information monitored in real time helps management to control and improve processes, minimize downtime, improve laden to unladen ratio and flow optimization, leading to minimizing OEE differences in the forklift fl eet by up to 20%. New forklift navigation, which helps drivers use the optimal route and avoid bottlenecks, has reduced the fleet’s total mileage by up to 10%.
Information about the utilization of forklifts revealed unused storage space. As a result of the optimization, the warehouse area was “expanded” by 20%, without any construction. It is also true that any process change can fi rst be tested in a digital twin, and thus simulated in a real model, thus avoiding negative side effects or failures.
Why choose Asseco CEIT RTLS?
- Higher accuracy
- Ability to work in a demanding and constantly changing environment
- Easy and fast scalability, tracking multiple objects and the ability to extend multi-shop system
- More than 1-year battery life warranty
50
50 cm accuracy and a 333-millisecond refresh rate
10 000
10,000 m2 covered area
66
66 receivers
70
70 traced objects
We are an innovative technology company with its own research and development center, bringing complex industrial solutions to the market.