Asseco CEIT AGV fleet
Asseco CEIT brings to customers a complete fleet of autonomous mobile devices, the so-called AGVs, with a high degree of customization, scalability and flexibility in logistics and production processes.
AGVs from Asseco CEIT are compatible and easily integrated tools not only for internal logistics, but also for complete production lines. To ensure a higher degree of automation, we use our forklift, under-run and tugger AGVs.
AGV according to use
Advantages of Asseco CEIT AGV

24/7 OPERATION
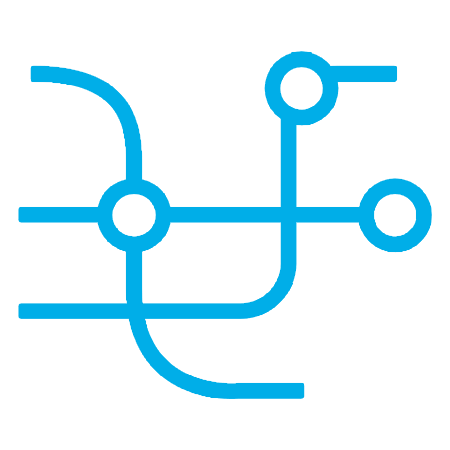
EASY INTEGRATION INTO EXISTING PROCESSES
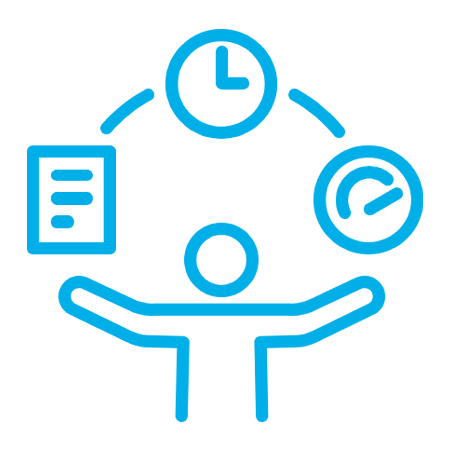
REDUCING OR REDIRECTING MANPOWER
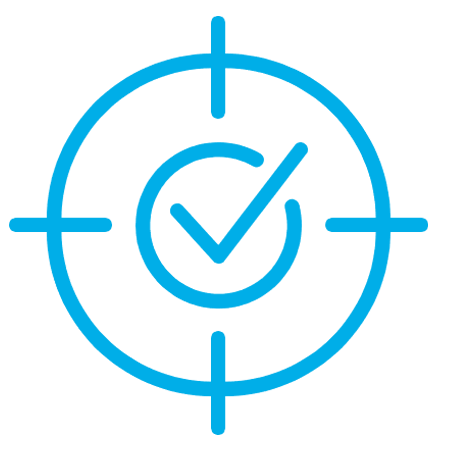
ERROR ELIMINATION AND DAMAGE CLAIMS
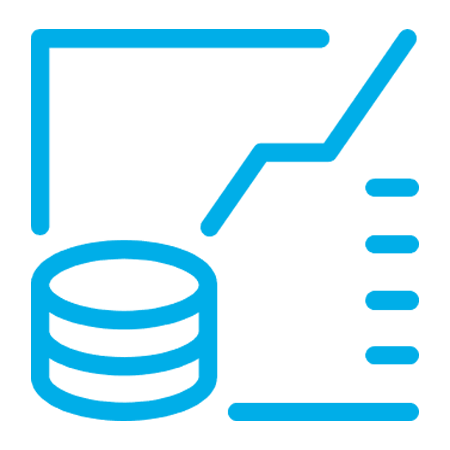
FAST ROI
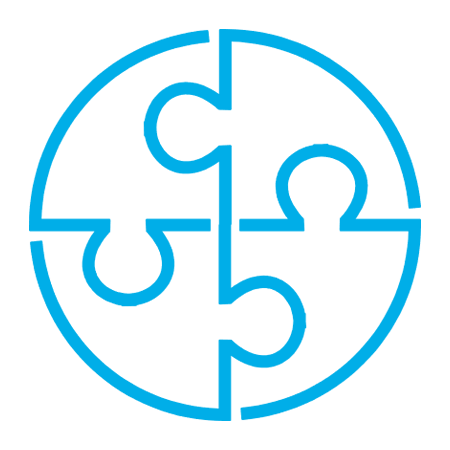